The Importance of Capacitors in Automotive Applications
Capacitors are one of the cornerstones of modern electronics—right up there with resistors and inductors. If you're building anything with electrons zipping around, odds are there's a capacitor (or fifty) somewhere in the mix. In fact, you’d be hard-pressed to find a modern electronic circuit that doesn’t rely on them in some way. They’re in filters, smoothing stages, timing circuits, energy storage systems—you name it.
But once you step into the automotive world, the game changes. Everything that might be “good enough” for consumer electronics goes out the window. In vehicles—where a single failure can mean the difference between safety and catastrophe—capacitors aren’t just important; they’re critical.
Unlike your smartphone or coffee maker, automotive electronics live a hard life. Think about it: under the hood or behind a dashboard, components face wild temperature fluctuations—from freezing mornings in Norway to blazing summer heat in Arizona. And then there's vibration. Constant, brutal, engine-driven vibration, plus the occasional pothole or fender bender that delivers an unexpected shock load.
In these conditions, not all capacitors survive. That’s why automotive-grade capacitors are designed to handle extreme thermal cycles, resist mechanical fatigue, and maintain their electrical properties over decades. Literally. Most automotive systems are designed with a 15–20-year service life in mind. And no, that doesn’t mean "replace it when it fails"—these parts are expected to just work, silently and reliably, for the life of the vehicle.
Capacitors in automotive systems aren’t decorative—they're functional lifelines. Whether it’s filtering out EMI from a power rail, stabilizing voltage levels in an engine control unit, or suppressing noise in an infotainment system, these humble components are constantly keeping chaos in check.
With the rise of electric vehicles, the demand on these components has only intensified. Higher voltages, more complex electronics, and tighter integration mean capacitors are working harder than ever. Now, it's not just about smoothing a 12V line—it’s about managing high-frequency noise on a 400V bus, or providing burst energy in hybrid drive systems. And let's not even start on fast-charging systems—those circuits can turn an average capacitor into toast if it isn’t specced correctly.
Sure, there are thousands of capacitor manufacturers around the world. And yes, you can buy a 100uF electrolytic for next to nothing from any number of vendors. But in automotive, nobody's gambling on unproven supply chains or fly-by-night factories. When safety, longevity, and legal liability are on the line, automakers and Tier 1 suppliers turn to the handful of trusted names with proven automotive pedigrees.
These manufacturers don’t just meet standards—they help write them. They’re running tests that go far beyond the datasheet. Thermal aging, accelerated life testing, vibration endurance, surge resilience—the lot. It’s a level of quality control that would make your average consumer electronics designer raise an eyebrow (or two).
Samsung Electro-Mechanics to supply MLCCs to BYD
Samsung Electro-Mechanics, a subsidiary of the South Korean conglomerate Samsung, has recently been given the green light to supply multilayer ceramic capacitors (MLCC) to BYD, the world's largest electric vehicle (EV) manufacturer. The move comes after Samsung Electro-Mechanics received final approval from BYD to supply large quantities of MLCCs and has officially begun the deliveries of the components.
The deal between Samsung Electro-Mechanics and BYD has been seen as a significant development in the automotive electronics industry, with Samsung Electro-Mechanics being one of the major players in the field. As a result of the deal, Samsung Electro-Mechanics is expected to secure a significant volume of MLCC shipments from BYD, which is expected to produce 55 million EVs this year. This figure is significantly higher than that of its main competitor, Tesla, which produced 1.3 million EVs last year.
The deal between Samsung and BYD comes at a time when the automotive industry is undergoing a major change, with the increasing adoption of electric vehicles and autonomous driving systems. As a result, the demand for automotive electronics components is also expected to increase, making companies like Samsung Electro-Mechanics a key player in the industry.
In addition to the deal with BYD, Samsung Electro-Mechanics has also been actively nurturing its business relationships with other Chinese EV manufacturers, including Xiaomi. The company has also been expanding its operations in the Philippines, where it has established a production facility for its MLCC components. The expansion of its operations in the Philippines is seen as a strategic move by the company, as it allows it to tap into the growing demand for automotive electronics components in the region.
The BYD–Samsung Deal — A Glimpse Into the Chinese EV Juggernaut
At first glance, the recent deal between Samsung Electro-Mechanics and BYD seems like a straightforward win-win. A trusted capacitor supplier locks in a high-volume customer, and a leading EV manufacturer shores up its supply chain for a critical passive component. But if we zoom out just a bit, this partnership reveals something far more telling about the global EV landscape—China’s meteoric rise as a dominant force in electric vehicles.
Historically, China hasn’t exactly been at the forefront of automotive innovation. Their vehicles were long considered inferior to Western or Japanese counterparts—lower quality, outdated designs, questionable reliability. But that narrative is collapsing fast. Case in point: BYD is set to manufacture up to 55 million EVs this year. That’s not a typo—it’s a level of scale that puts the rest of the industry on notice.
To put things in perspective, Tesla, once hailed as the trailblazer and supposed gold standard of EVs, produced around 1.3 to 1.5 million vehicles last year. Yes, Tesla is still a technological leader in many respects, but when it comes to raw production volume, they’ve been completely outpaced. And while Elon Musk is busy posting memes and promising robotaxis, BYD is churning out vehicles like clockwork.
But how did we get here? Well, that’s the billion-dollar question. How does a country with little automotive legacy scale to tens of millions of high-tech vehicles seemingly overnight?
- Is it a result of cheap labor and government-subsidized infrastructure?
- Are we seeing environmental and ethical shortcuts that would be unacceptable in Western markets?
- Or has China simply optimized its industrial machine to out-compete legacy automakers who’ve grown too bloated to move quickly?
The truth is, we don’t know the full story yet—and anyone claiming to is likely selling something. But it’s reasonable to be skeptical. Mass production at this scale doesn’t come without cost. The question is: who’s paying the price? Is it the environment? Factory workers? Or, in the long term, consumers who may find themselves driving vehicles made under questionable standards?
Let’s be clear: China can build road-legal vehicles, and BYD’s global presence proves they’re meeting at least the minimum thresholds for safety and compliance. But meeting standards isn’t the same as building trust.
As engineers, designers, and manufacturers, we need to ask hard questions. When we source components, partner with suppliers, or integrate products built at massive scale in record time, we should do so with both eyes open and our conscience intact. It’s not about nationalism or protectionism—it’s about responsibility.
You may also like

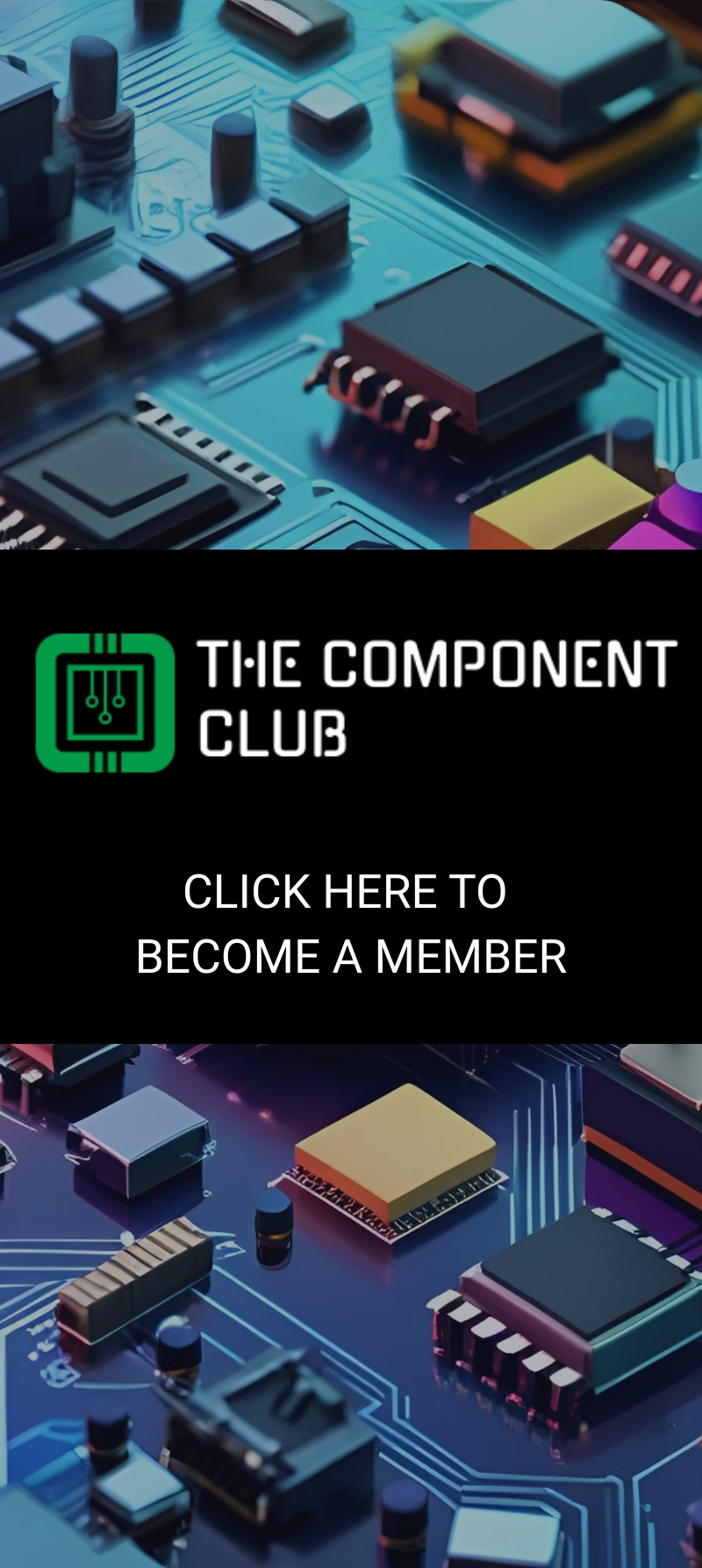